It wasn’t there one day, and by the end of the next, there it was. It may look like a big rectangle of steel, and it is. If you’ve been at the corner of 5th and Roosevelt streets this past month, you’ve noticed the Upcycle Living model home on the northeast corner. Yes, it’s a rather large hunk of steel shipping containers stitched together. Yes, it is a working, functional home. And yes, people can live in these things.
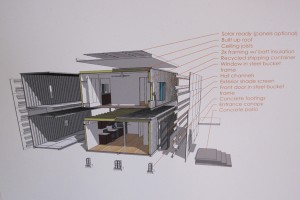
The shipping containers can be pieced together seamlessly.
“Our whole mantra is ‘affordable, conscious living,’” says Upcycle Living partner Ashton Wolfswinkel. The Chandler native and his Tucson counterpart, homebuilder Jason Anderson, met at University of Arizona and later began collaborating when Anderson moved to the Valley.
When Anderson arrived, he started working on a design-build project for a client in North Phoenix in spring 2009. Having spent time in Europe, where “upcycled” architecture is more commonplace, Anderson had a few ideas up his sleeve.
“The client wanted to do a master suite addition, but he just didn’t have the budget to do it,” Wolfswinkel recalls. “So, Jason pitched the idea of using shipping containers. We attached three containers to the main house — bedroom, his-and-her closet and bath — about 1,000 square feet of living space.”
Wolfswinkel was never skeptical of Anderson’s idea to use upcycled materials.
“He pitched me the idea, and I sat on it for a couple of days, then said, how do we do it? Let’s go.”
Wolfswinkel’s background is in property management and real estate development. After unsuccessfully trying to “green” his father’s mobile home business, he was itching for something new and exciting. Modular, sustainable housing seemed a natural next step. He and Anderson found a space near 15th Avenue and Lower Buckeye Road to execute the concept.
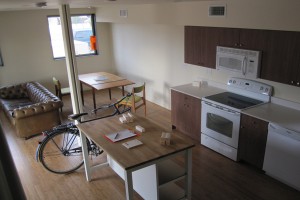
The living room and kitchen have a modern feel.
“The benefit to modular housing is building in the controlled location — all your equipment and supplies are already there,” Wolfswinkel explains. “You can control the quality easier in that central location where everyone is working. This process takes conservatively six to eight weeks, ideally four weeks. If we can build one of these in three to four weeks, that’s really good.”
And, the benefits are many: low initial cost, shrunken bills and a greatly decreased carbon footprint. Ninety-five percent of the building is done at the Upcycle Living facility, then the finishing touches are completed at the home site.
“We put each container on a flatbed truck, ship it and drop it in place,” Wolfswinkel says. “It’s about a two- to three-day turnaround install, assuming the foundation is there — which are 18-inch piers that sit on the corner of each box. Then you just hook up electrical and sewer, and with a little tape and texture, you’re ready to go. Two or three days, and you have a house.”
The containers themselves come from various ports around the West — Seattle, Long Beach, Oakland, Houston — and businesses in those ports have been supportive of the reuse of the containers, saving valuable port space. They welcome Upcycle Living taking the boxes, and they come cheap.
By not pouring the foundation, the company saves more money. The steel structure is the bones, so money, time and materials are saved in that way. In turn, this savings allows for upscale, efficient features throughout: dual-flush toilets, bamboo floors, Energy Star appliances, steel staircases, recycled carpets, recycled countertops, low-VOC recycled cabinets, solar panels, urban gardens, gray water reuse systems and more.
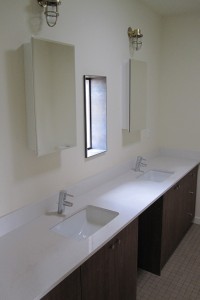
An example of a fully customizable bath
Upcycle Living is focusing on two drastically different areas for its housing: urban cores to increase density — something that could be very beneficial to neighborhoods full of empty lots in Downtown Phoenix— and rural areas away from cities.
Wolfswinkel notes that he’s received good feedback from people from the High Country; they’re looking for homes that are fireproof in their heavily wooded areas. Upcycle Living is licensed to build and install in Arizona, but they’ll ship anywhere. Subcontractors can easily install the structure and get it running. On top of that, the company looks to source as much material as it can from within the state. Other, harder-to-come-by materials come from neighboring states.
But, does it feel like a home? Tours of the model have yielded lots of enthusiastic responses. The model itself is surprisingly homey and airy, at around 1,200 feet, with two bedrooms and three baths laid out rather cleanly. From the outside, it really doesn’t look much different than the Catherine Arms and PRD-845 projects in Downtown Phoenix. In other words: Steel is in!
The affordability factor could be a key in increasing urban infill and density throughout Downtown Phoenix. Young couples can make their first home an Upcycle Living home. Cheap dirt lots can house shiny new boxes and strengthen neighborhoods. People who want an affordable second home in the urban core can custom-design the floor plan of their dreams with Anderson and Wolfswinkel — he likens arranging the shipping containers to playing with Legos — the possibilities are endless.
As for the affordability: It hasn’t quite been priced out, but Wolfswinkel estimates the model home as it stands would go for about $85-90,000. That should leave some dough for some nice, eco-friendly irrigation and landscaping, solar panels, façade work and more. Not too shabby.
So, don’t be so sure that steel box on Roosevelt Street is something to avoid. Being ultra green and affordable is one thing, but having a welcoming home is another. Luckily, Upcycle Living offers all that and more.
For more information on Upcycle Living, contact Ashton Wolfswinkel at 602.989.8162 or ashton@upcycleliving.com. The model on Roosevelt and 5th streets will remain in the coming months. Call to schedule a showing or visit during First Friday open houses.
So…does anyone live in the one now? Why not?
What about insulation from the triple-digit summers? That included?
Those are good questions. The company is young. They’re just getting started with this concept, but I give the example of the 1,000-sf addition in North Phx. There’s a ton of interest. They’ll be popping up a lot of places in 2010. We’ll keep you posted.
As for insulation, obviously it’s not just steel wall and insides. There’s drywall on the inside and insulation. They actually have several different R-value insulation options depending on what you’d like to spend. There’s also a ceramic paint that’s offered for the exterior that deflects the heat.
Very cool. I’d live in one. Seems a similar, less expensive version of Vine Saccento’s V2 concept.
I assume soundproofing would also be included, especially once you build an enclave of these, back to back, on some lot.
If you haven’t already, I recommend checking out the model. I think you’ll be very surprised.
I’m with Tyler on this one: unless they can successfully mitigate Phoenix’s summer heat, they have completely no future here in the Valley. It would seem that their metal exterior would make any insulation efforts work significantly harder.
Time’ll tell.
How do we make an appointment to tour.?
Thank you, ken
thx